發佈日期:2017/5/8
發佈單位:iST宜特
還記得90年代風靡一時的電視影集霹靂遊俠與他的搭檔-霹靂車夥計,以及它的經典台詞:
霹靂車,尖端科技的結晶,是一部人性化的萬能電腦車。出現在我們這個無奇不有的世界,刀槍不入,無所不能。
在當時的時空環境背景下,許多人都認為這只是單純的科幻片,憑空想像出來的。而隨著科技的日新月異;當時所不能實現的科技產物在現今的國際著名車廠如Tesla、M-Benz、BMW、TOYOTA等均已開發出多款AI無人駕駛智慧汽車。其功能包含自動駕駛、自動停車、碰撞警示、自動煞車等多項功能。而這些裝置的內部電子元件在安裝之前,必須經過一連串嚴苛的可靠度測試來確保產品品質是無故障或損壞的,以保障使用者的人身安全。
汽車產業原本為一個非常封閉的環境,國際車廠並不會將產品Cost Down視為重要的任務,因為汽車是與人類生命財產有關的行業,產品設計的不良或可靠度的缺陷將會造成車廠巨大的賠償,因此車廠不會輕易的去更換供應商。但近年來「AI智慧電動車」與「ADAS」的崛起,汽車電子佔車價的比重逐步提升到40-50%,這兩個汽車新發展面向,使得車廠必須開始跳脫既有的供應鏈,開始尋找合適的電子產品供應鏈。從2017年全球汽車銷售量排行榜來看,前七大車廠的銷售量已經佔了全球60%的比重,這代表市場是非常集中的,如何擊退競爭者進入國際車廠的供應鏈,無非是現今電子廠商所面臨的重要課題。
在消費性電子產品的產業中,產品的生命週期通常不長,3-5年內就會有汰舊換新的情況發生,這也造就了Time to Market的能力與優勢,許許多多的新創產業就在此中萌芽發展。然而轉換到汽車產業,新技術往往不會放入最暢銷的車款上,而是把最成熟、可靠度品質最佳的產品導入。筆者認為,如果你是剛萌芽求生存的公司,應該將產品朝向副廠零組件(AM, After Marketing)努力;如果你的目標客戶或是終端客戶為車廠/Tier 1,那麼提高產品的可靠度將會是唯一路徑。
該如何提升電子產品可靠度? 本文將從國際規範 SAE J1211 與 ISO 26262 都強調的規格需求與驗證結果-V型曲線(參見圖一)來探討,解析汽車電子零件/元件設計與驗證要點,並加入筆者實際在宜特與德凱宜特實驗室服務的實戰經驗,期望協助將加入智慧汽車供應鏈的廠商能夠掌握要點。
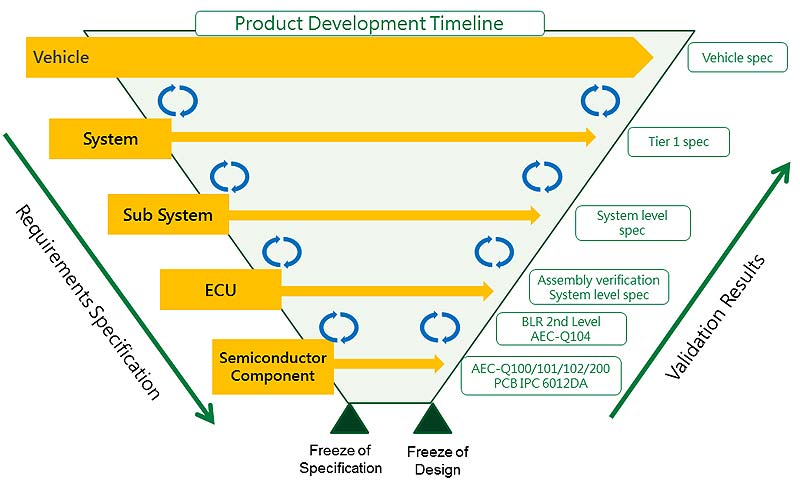
圖一:汽車電子零件/元件設計與驗證流程 (資料來源: SAE J1211)
一、國際可靠度品質車規驗證五大步驟
當車廠要開發一個產品與功能時,將會定義系統功能->子系統功能->該採用的電子控制單元(ECU)->需要使用的半導體元件,規格由左至右、由上而下;但在進行驗證時則需由下而上,一步一步完成驗證需求,正所謂「基礎不牢,地動山搖」,從最源頭確認品質起,將會是產品達到高可靠度的不二法門。如不遵循V型曲線,當產品發生失效狀態下,就無法釐清是上一段產品問題,還是製程問題,或是自己設計不良所導致。
- Step 1:Component level – 主動元件(IC)符合AEC-Q100需求、離散元件符合AEC-Q101、LED符合AEC-Q102(2017年新版)、多晶片模組MCM符合AEC-Q104要求(2018年新版) 、被動元件符合AEC-Q200
- Step 2:PCB level -印刷電路板(以下簡稱PCB)通過IPC-6012DA驗證
- Step 3:Board level – 考量元件上板後的焊點可靠度(BLR, Board Level Reliability)
- Step 4:Board level – PCBA製程品質驗證確認
- Step 5:System level -從系統模組到Tier 1 / 品牌車廠的標準規範
(一) Step 1: Component level: AEC-Q系列
對車用ICs可靠度驗證而言,美國在1994年即由克萊斯勒(Chrysler)、福特(Ford)以及通用汽車(GM)三大汽車廠發起成立汽車電子委員會(Automotive Electronics Council-簡稱AEC)。AEC建立車用電子零組件的品質控制標準,符合AEC規範的零組件均可被Chrysler、Ford與 GM三家車廠同時採用,因而促進了零組件製造商交換其產品特性數據的意願,並推動了汽車零件通用性的實施,為汽車零組件市場的快速成長打下基礎。
近年來國際車廠於安全相關的ECU上,將AEC-Q100制定為強制性的主動元件需求,AEC-Q200詢問度亦逐步提高,未來也會轉化為強制性的需求,筆者呼籲廠商可提早因應。對於LEDs Component, AEC也於2017年頒布了AEC-Q102,已成為車用LED的聖經。
(二) Step 2: PCB level- PCB板通過IPC-6012DA驗證
印刷電路板(Printed circuit board,簡稱PCB)是主被動元件的溝通橋樑,當元件故障時可透過Re-work更換,但不可能移除所有元件後再更換PCB,因此不得不說PCB為汽車電子零元件中的關鍵零件。
車用PCB以往並無特殊的驗證手法,多遵照IPC-6012進行驗證,由於車用電子市場的崛起,PCB製造業者積極搶食這塊大餅,IPC(國際電子工業聯接協會,簡稱IPC)不得不重視此問題,特別於2016年頒布了首份針對車用PCB的驗證及允收規範IPC-6012DA,其中包含了溫度衝擊耐久試驗(Thermal shock endurance Testing)、高溫耐久試驗(High Temperature Endurance Testing)、高溫高濕儲存試驗(High Temperature & Humidity Storage Testing)、陽極細絲導通試驗(Conductive Anodic Filament,簡稱CAF Testing)、表面絕緣電阻試驗(Surface Insulation Resistance,簡稱SIR Testing)…等。這份也成為車廠與Tier 1對於PCB可靠度驗證的重要參考法規。
(三)* Step3 :Board level-車用元件上板後的焊點可靠度(板階可靠度測試,Board Level Reliability,簡稱BLR)
板階可靠度(BLR),是國際間常用來驗證IC元件上板至PCB之焊點強度的測試方式,是目前手持式裝置常規的測試項目。而隨著汽車電子系統的複雜度提升,更多的IC元件被運用在汽車內,BLR遂逐步成為車電重要測試項目之一,不僅Tier 1車廠BOSCH、Continental、TRW對此制定專屬驗證手法,令人注意的是AEC汽車電子協會近期最新出爐的AEC-Q104,明確定義了車用電子的板階可靠度試驗(Board Level Reliability)項目,雖然項目僅有BLR TCT(溫度循環)、Drop(落下)、Low Temperature Storage Life(簡稱LTSL)、Start Up &Temperature Steps(簡稱STEP)等,尚未能完全貼近Tier 1的客戶規範,但卻是車用板階可靠性通用標準發展的一大步。下列表格為Tier 1大廠針對Board Level的測試需求(表一)。
Test Item A Company B Company C Company RTC
TMCL
(BLR
TCT)◆ -40~125℃ @ 2,000~4,000 cyc.
◆ 30 mins. dwell time
◆ Dual chamber(Air to Air)◆ -40~125℃, @ min 2,000 cyc
◆ 10 mins. dwell time.
◆ 10 ≤ ∆T/∆t ≤ 20 K/min.◆ -40~125℃ / -40~150℃ @ 3,000 cyc.
◆ 10 mins. dwell time.
◆ 30 mins transfer timePTC ◆ -40~105℃ @ 2,600 cyc
◆ T on/off = 5mins. 10mins./cyc.NA NA Vibration ◆ 100Hz~2,000Hz @ 5.02 PSD
◆ RMS acceleration : 97.7m/s2.
◆ Random Vibration + Temp.◆ 20Hz~2,000Hz @ 0.1 PSD,
◆ RMS acceleration :189.4~818m/s2.
◆ Sine sweep or random VIB.NA Drop NA ◆ Direction C+/C-
◆ 1,000G @ 1.4ms◆ Direction C-
◆ 1500G, 0.5ms, 60 dropBending ◆ Deflection d=1,0mm, 20sec
◆ Bend to failNA ◆ Displacement d=2.0mm, 100cyc.
◆ Displacement d=4.0mm, 100cyc.表一: 汽車Tier 1大廠Board Level測試需求
1. 歸納在宜特與德凱宜特實驗室中,常見車電晶片Board Level焊點失效五大主因:
(1) 焊點大小與排列方式
(2) 焊點合金成分
(3) PCB設計方式與材料選擇
(4) Reflow溫度與Flux殘留
(5) 焊點周圍的填充物。(參見圖二)其中的(2)、(3)、(5)項會延伸到另一個問題,就是熱膨脹係數(Coefficient of Thermal Expansion)。車用晶片在運作中可能產生很高的溫度,不同材料熱膨脹係數不同,會產生不同的變形量,除上述提到的振動應力外,溫度產生熱脹冷縮會對於焊點有拉扯與擠壓的破壞能力,如果晶片材料能選擇較相近的熱膨脹係數越接近,溫度產生的應力將大大減少。電腦與手機等產品的保固期間大約是2~5年,由於一般車用晶片使用年限會長達10~20年,測試條件須謹慎評估,所以在晶片規劃初期,可先將這幾個因子考量進去,汽車產業要求的安全與可靠度標準遠比電腦和手機等產品嚴格,除可提高晶片壽命之外,對於失效分析後的改善時程與費用皆能有所提升。
圖二:汽車電子Board Level焊點失效五大關鍵因素
2.相較於消費型電子產品Board Level測試條件,是否可以參考或沿用至車用產品?
以上筆者在宜特與德凱宜特實驗室時,客戶最常詢問的問題之一。答案是不行的。因為這些系統模組導入車輛設計之中,車載平台使用的環境與結構大不相同,汽車在啟動後,所有晶片都會開始承受振動、機械的應力與外在惡劣環境,若使用消費型電子產品測試條件後,在真實使用環境可能會發生所謂的早夭現象。以振動測試說明,手持式產品振動模式以一般運輸為主,大致上包含陸、海、空運模擬。而車用振動測試,因晶片會長時間暴露在外在環境,必須考量溫度與濕度的耐用程度,寒帶國家與熱帶國家使用的環境就不一樣,密閉空間在太陽照射下可能達到100℃,引擎周圍溫度更高達150℃,必須確認晶片是否能抵禦溫度與震動的能力。所以為了模擬更真實的環境,振動過程會將環境條件加入測試,這就是我們常聽到的複合式振動測試。除振動與溫度之外,還有針對晶片焊點接合強度進行分析,例如:晶片推力、拉力、循環式彎曲等等,這些都是要確保所有焊點能保障駕駛者的安全。
(四) Step 4:Board level - PCBA製程品質驗證確認
歐盟2006年7月開始實施RoHS,在電子產品上限制使用鉛(Pb),含量需小於1000 ppm。在當時電子產品使用錫鉛銲錫已經超過50年以上歷史,導入無鉛製程中,無論設備、測試方法、產品品質與可靠度等議題必須重新進行檢視與確認。焊接材料從錫鉛轉為無鉛錫膏後熔點由183℃提升至217℃,溫度的提升導致焊點硬度變硬、變脆、耐疲勞性差,焊點缺陷多容易造成錫鬚等問題,因此掌控製程良率的難度大幅提升。當時因醫療、國防、車用電子的應用上,對於可靠度需求極高,所以導入的腳步較消費性的電子產業慢很多。
在2007年版的AEC-Q100 Version G尚未有無鉛(Pb Free)的驗證需求,不過AEC在2009年發布了Q005(PB-FREE TEST REQUIREMENTS),正式面對了無鉛製程的轉換;且2014年在進行AEC-Q100的改版作業中(Version G->H),加入了無鉛測試的驗證要求包含了焊錫性測試(Solderability)、焊錫耐熱試驗(Solder Heat Resistance)以及錫鬚試驗(Tin Whisker),從此汽車電子毅然而然跟上環保的腳步。
而廠商在消費性電子產品導入無鉛過程中,累積了非常多的經驗,克服了各式各樣的難關,因此在進入車用的階段相對有經驗,下圖三為車用無鉛驗證流程圖(取自德凱宜特實驗室)。
圖三:車用無鉛驗證流程圖(資料來源:德凱宜特實驗室)
近年來不只車載資訊系統導入無鉛的製程,筆者所任職的宜特與德凱宜特實驗室也接獲國際Tier 1廠商送出ABS、SRS的安全功能關鍵ECU進行驗證,這也代表站在最高可靠度殿堂上的汽車產業,對於人身安全核心的電子零組件已將無鉛製程的可靠度達到另外一個境界了。
在宜特與德凱宜特實驗室與Tier 1 接觸經驗上,可以發現各區域的要求會有不同的重點:
- 歐/美車廠與Tier 1重視產品使用的壽命,用產品生命週期與加速測試手法來擬訂測試計畫,如高溫加速模型(Arrhenius)、高溫高濕加速模型(Hallberg-Peck)、溫度循環加速模型(Coffin-Manson)。
- 美系特別要求高加速壽命試驗(High Accelerated Life Testing,簡稱HALT),利用Test to Failure來找出產品的設計缺陷,在設計驗證階段就先將設計的缺陷改善(參見圖四)。
- 亞洲(日韓)要求離子遷移(Migration)與錫鬚的驗證(Tin Whisker)。筆者推測,亞洲對於這類電化學的驗證,都是透過長時數的測試來進行,而非採用加速的方式進行驗證,因此這樣的測試結果讓人感受到實際產品擁有較長的車用電子產品使用壽命。而歐系講究環保議題,使得產品壽命上的實際感受不如亞洲車廠與Tier 1。
圖四:美系車廠高加速壽命(HALT)試驗圖
(五) Step 5:System level – 從系統模組到Tier1 / 品牌車廠的標準規範
系統模組的驗證需求大致可區分為三個階段:
- 求生存:此時公司正面臨生死存亡的關鍵時刻,能將產品用最低價最快速的方式投入市場才能足以生存,在這個階段並無品質與可靠度可言。
- 副廠品牌:公司已有所規模,想要逐步建立品牌價值,這時多參考國際車用規範進行品質驗證,而業界最普遍且通用性最廣的則為ISO 16750(繁體版CNS 15481、簡體版GB/T 28046、日文版JASO D014),內含四大類的驗證,電性負載、機械負載、氣候負載、耐化學溶劑負載。
- 車用正廠零組件:此時唯有通過車廠廠規或是Tier 1廠規,並無其他二路可選。
二、結語
以筆者在宜特與德凱宜特實驗室所接觸的汽車供應鏈實戰經驗中建議,要在汽車這個產業長久生存,需跳脫既有的消費性電子產業思維,對於品質與可靠度的要求是沒有任何妥協的餘地,價格是放在最後的考量,車廠對於新的產品導入可能有長達3~5年驗證期,對於產品的售後維修備料,更可能要求達20年之久,當決定跨入汽車產業之路,經營者必須更有耐心與決心。若您對汽車電子驗證有相關需求,請洽宜特+886-3-579-9909分機6406莊先生(Daniel) Email: web_BLR@istgroup.com 或 德凱宜特+886-3-579-5766分機7201陳先生(Wangchu) Email: web_SRE@dekra-ist.com
此篇同步刊登於
EEtimes電子工程專輯2018年5月號
關於作者:
宜特科技 可靠度工程處 板階可靠度工程部經理
莊家豪
德凱宜特 技術行銷室 資深技術經理
陳旺助